work in process inventory balance formula
Total Manufacturing Costs Beginning WIP Inventory Ending WIP Inventory COGM. Beginning WIP Inventory Ending WIP Inventory Manufacturing Costs COGM.
What Is Work In Process Wip Inventory How To Calculate It Ware2go
If your ending WIP equals 20000 you have 20000 times.
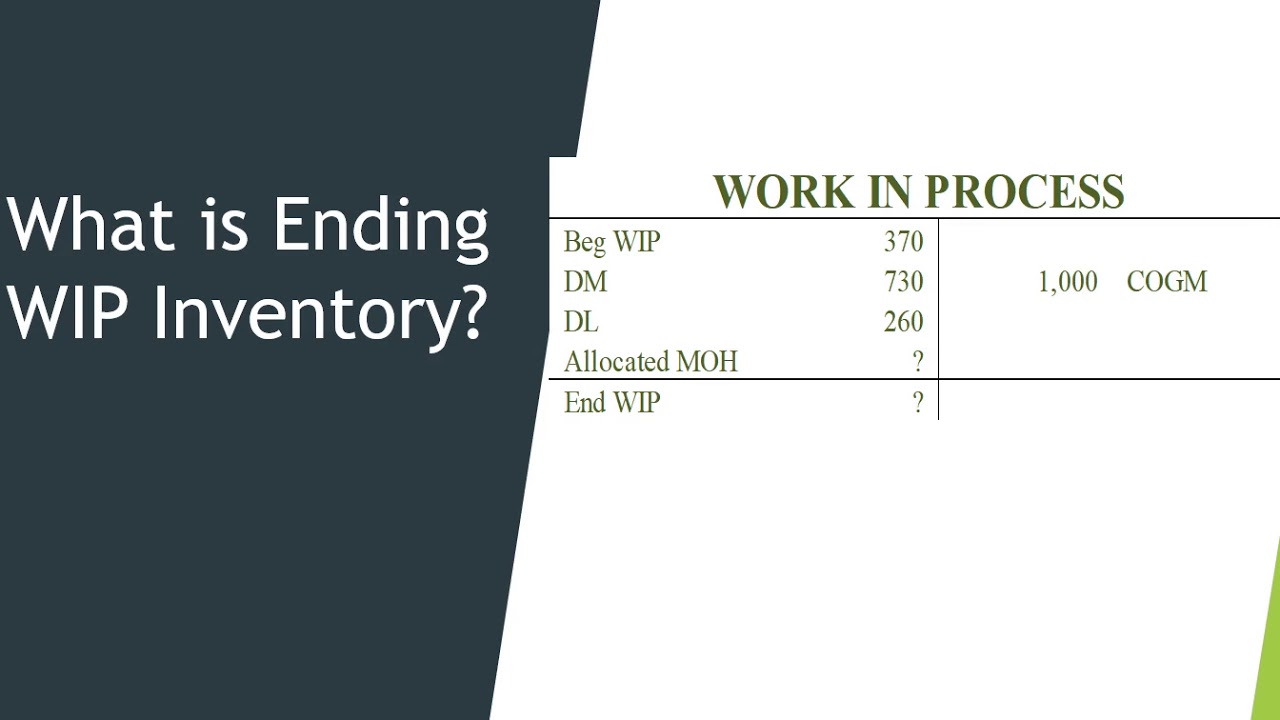
. The WIP formula. Ending WIP Inventory Beginning WIP Inventory Manufacturing Costs - Cost of Finished Goods. The ending balance of inventory for a period depends on the volume of sales a company makes in each period.
The calculation of ending work in process is. Imagine BlueCart Coffee Co. Beginning WIP Manufacturing costs - Cost of goods manufactured.
Whether to reference us in your work or not is a personal decision. Higher sales and thus higher cost of goods sold leads to draining the inventory account. Once you have calculated your starting in-process inventory manufacturing expenses and cost of made items you can quickly ascertain how much work in process inventory you have.
The formula for COGM is. Ending WIP Inventory Beginning WIP Inventory Manufacturing Costs COGM. Lets use a best coffee roaster as an example.
Total Cost of Manufacturing Beginning Work in Process Inventory Ending Work in Process Inventory Cost of Manufactured Goods. Keep in mind this value is only an estimate. Total Manufacturing Costs Beginning WIP Inventory Ending WIP Inventory COGM.
WIP is calculated as a sum of WIP inventory total direct labor costs and allocated overhead costs. In this case for example consider any manufactured goods as work in process. Ending work in process.
Force can be calculated with the formula Work F D Cosineθ where F force in newtons D displacement in meters and θ the. Once all of the above variables are determined the formula to calculate the WIP inventory is as below. This means that Crown Industries has 10000 work in process inventory with them.
How to Calculate Ending Work In Process Inventory. Add the new purchases and subtract the Cost of goods sold. It is necessary to calculate two rates for materials one for Material 1 and another for Material 2 to evaluate production expressed in equivalent units.
The ending work in process is now calculated using the work in process inventory formula as follows. For the exact number of work in process inventory you need to calculate it manually. Multiply the balance of work in process by 020.
Determining the balance of Inventory. The proportion of the unit cost is the overhead of 10 divided by the 50 total cost or 020. It is obvious that partly completed units in Process II are partly completed only in respect of work to be done in Process II.
10000 300000 250000 60000. Therefore they are 100 complete as regards Material 1. So to calculate ending inventory for the period we will start will the inventory which is currently listed on companys balance sheet.
Ending WIP Beginning WIP Materials in Direct Labor Overheads - COGM Ending WIP 25000 40000 10000 5000 - 45000 Ending WIP 35000 Again this can be summarized as follows. However by using this formula you can get only an estimate of the work in process inventory. Regardless of the type of inventory control process you choose decision-makers know they need the right tools in place so they can manage their inventory effectively.
Ending WIP Inventory Beginning WIP Inventory Manufacturing Costs Cost of Finished Goods. Work in process inventory 60000. Take a look at how it looks in the formula.
The WIP figure indicates your company has 60000 worth of inventory thats neither raw material nor finished goodsthats your work in process inventory. Furthermore calculating the COGM is done by adding the total manufacturing costs to the beginning WIP inventory and subtracting the ending WIP inventory. Adding the totals of these categories will give you your current work in process inventory.
Work-in-Progress Vs Work-in-Process Inventory. The work in process formula is. Ending Inventory Beginning Inventory Inventory Purchases Cost of Goods Sold.
8000 240000 238000 10000. Work in process inventory includes all raw goods production expenses and labor costs associated with producing merchandise inventory. Ending WIP Beginning WIP Costs of manufacturing - costs of goods produced.
The amount of ending work in process must be derived as part of the period-end closing process and is also useful for tracking the volume of production activity. Suppose you have allocated 10 per widget for overhead and the direct labor and materials costs total 40 giving a unit production cost of 50. There are things it doesnt consider like waste spoilage downtime scrap and MRO inventory.
Part 1 of 3. The formula for this is as follows. Has a beginning work in process inventory for the quarter of 10000.
Your WIP inventory formula would look like this. Also known as COGM the cost of manufactured goods is the total costs incurred in the making of a final product. You have to know the final COGM to calculate the current WIP inventory value.
Ending Inventory Beginning Balance Purchases Cost of Goods Sold. The beginning WIP inventory cost refers to the previous. The difference between the sum of the beginning work in process and the costs of manufacturing is the ending work in process.
WIP inventory is estimated using the following formula. Work in Process Inventory Formula Therefore the formula from which a business can calculate their COGM using work in process inventory costs can be displayed like this. Using this WIP formula businesses can calculate how much work in process inventory they will have left over at the end of the accounting period.
How To Calculate Ending Inventory The Complete Guide Unleashed Software
Beginning Work In Process Inventory Business Accounting
Wip Inventory Definition Examples Of Work In Progress Inventory
Ending Inventory Formula Calculator Excel Template
Manufacturing Account Format Double Entry Bookkeeping
Work In Process Inventory Formula Wip Inventory Definition
Inventory Days Formula How To Calculate Days Inventory Outstanding
Ending Work In Process Double Entry Bookkeeping
Inventory Formula Inventory Calculator Excel Template
Work In Progress Meaning Importance Accounting And More
Manufacturing And Non Manufacturing Costs Online Accounting Tutorial Questions Simplestudies Com
Cost Of Goods Manufactured Formula Examples With Excel Template
Cost Of Goods Manufactured Formula Examples With Excel Template
Cost Of Goods Manufactured Formula Examples With Excel Template
Work In Process Wip Inventory Youtube
Work In Progress Wip Definition Example Finance Strategists
Manufacturing And Non Manufacturing Costs Online Accounting Tutorial Questions Simplestudies Com